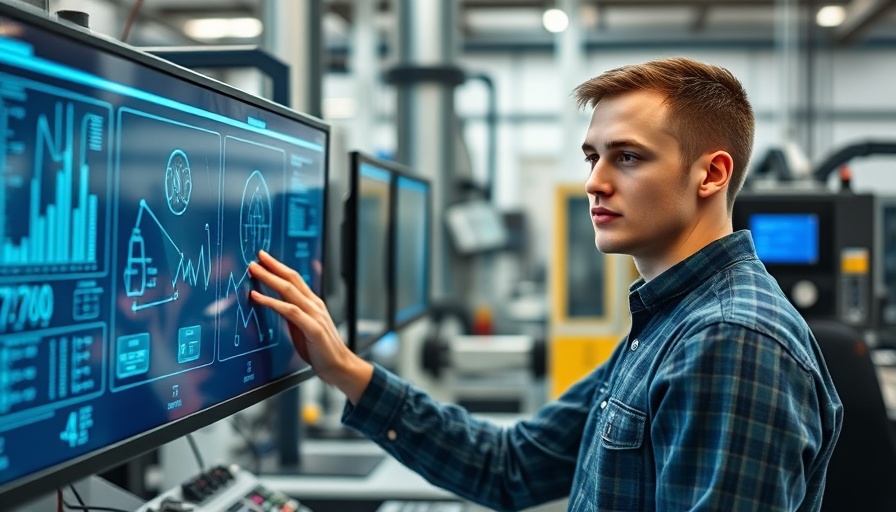
Revolutionizing Titanium Alloy Production with AI
In recent advancements, researchers at the Johns Hopkins Applied Physics Laboratory (APL) and the Whiting School of Engineering have unveiled groundbreaking methods to enhance the production of titanium alloys using artificial intelligence (AI). This innovative approach addresses the challenges of producing high-performance titanium parts, which are critical for industries like aerospace, shipbuilding, and medical technology. The ability to manufacture these alloys more quickly and with improved strength could lead to substantial improvements across multiple sectors.
Historically, creating titanium alloy components, especially the widely-used Ti-6Al-4V, has involved resource-intensive processes with lengthy trial-and-error methodologies. Engineers have often been limited by the need for meticulous optimization of various manufacturing conditions, from laser power to printing speed, greatly slowing down production. However, the integration of AI technologies into manufacturing processes has opened new horizons in efficiency and effectiveness.
A Game-Changer in Engineering Process
The research team has leveraged AI-driven models to navigate previously uncharted manufacturing conditions for laser powder bed fusion, a pivotal technique in 3D metal printing. Their findings, as published in the journal Additive Manufacturing, demonstrate a significant extension of processing parameters, enabling the production of denser, higher-quality titanium components with customizable mechanical properties.
Co-author Brendan Croom noted that, for years, the industry operated under the misconception that certain processing parameters were immutable, leading to a narrow scope for experimentation. With AI's assistance, these assumptions are being challenged, revealing new processing capabilities that enhance material strength while also accelerating production speed.
AI's Role in Material Science: Beyond Expectations
At the core of this innovation lies a technique known as Bayesian optimization, where AI predicts the most effective experimental conditions based on prior outcomes. This computational accuracy permits scientists to explore thousands of material combinations virtually faster than manual tests would allow.
By employing this methodology, researchers discovered processing conditions that had previously been deemed unstable, enabling improvements in both speed and material performance. Morgan Trexler, program manager at APL, emphasized the importance of these advancements in meeting urgent demand across various sectors, particularly those facing evolving operational challenges in defense and technology.
Broader Implications: Transforming Industries
The potential applications of this research are vast. Improved methods of producing stronger, lighter titanium components stand to revolutionize shipbuilding, aviation, and even the medical device industry. The speed of production can significantly influence the ability to respond to market demands and enhance operational readiness in key sectors.
Moreover, this research aligns with ongoing efforts to advance additive manufacturing techniques, striving not just for faster production but also for achieving superior quality through tailored material properties. The intersection of AI and material science marks a turning point, with implications that extend beyond titanium alloys into new materials and innovative manufacturing approaches.
The Bright Future Ahead in Additive Manufacturing
As AI technologies continue to evolve, the prospect of using real-time in situ monitoring during the production process could enhance quality assurance and reduce waste. The ultimate goal is a manufacturing paradigm shift towards seamlessly integrated systems, capable of adjusting dynamically while producing titanium alloys and similar materials.
In conclusion, the recent advancements at Johns Hopkins highlight the immense potential of leveraging AI in metallurgy. As researchers keep pushing the boundaries, we could see a revolution in how industries produce complex materials that meet the demanding requirements of the modern world.
With these trailblazing capabilities, now is the time for industries to invest in AI-enhanced manufacturing technologies, ensuring they stay at the forefront of innovation.
Write A Comment